Our Process
It all starts with dirty sorted brass. We source our brass from a processor that obtains brass from reputable primarily indoor ranges, so we are certain that 99% of our brass has only been fired once.
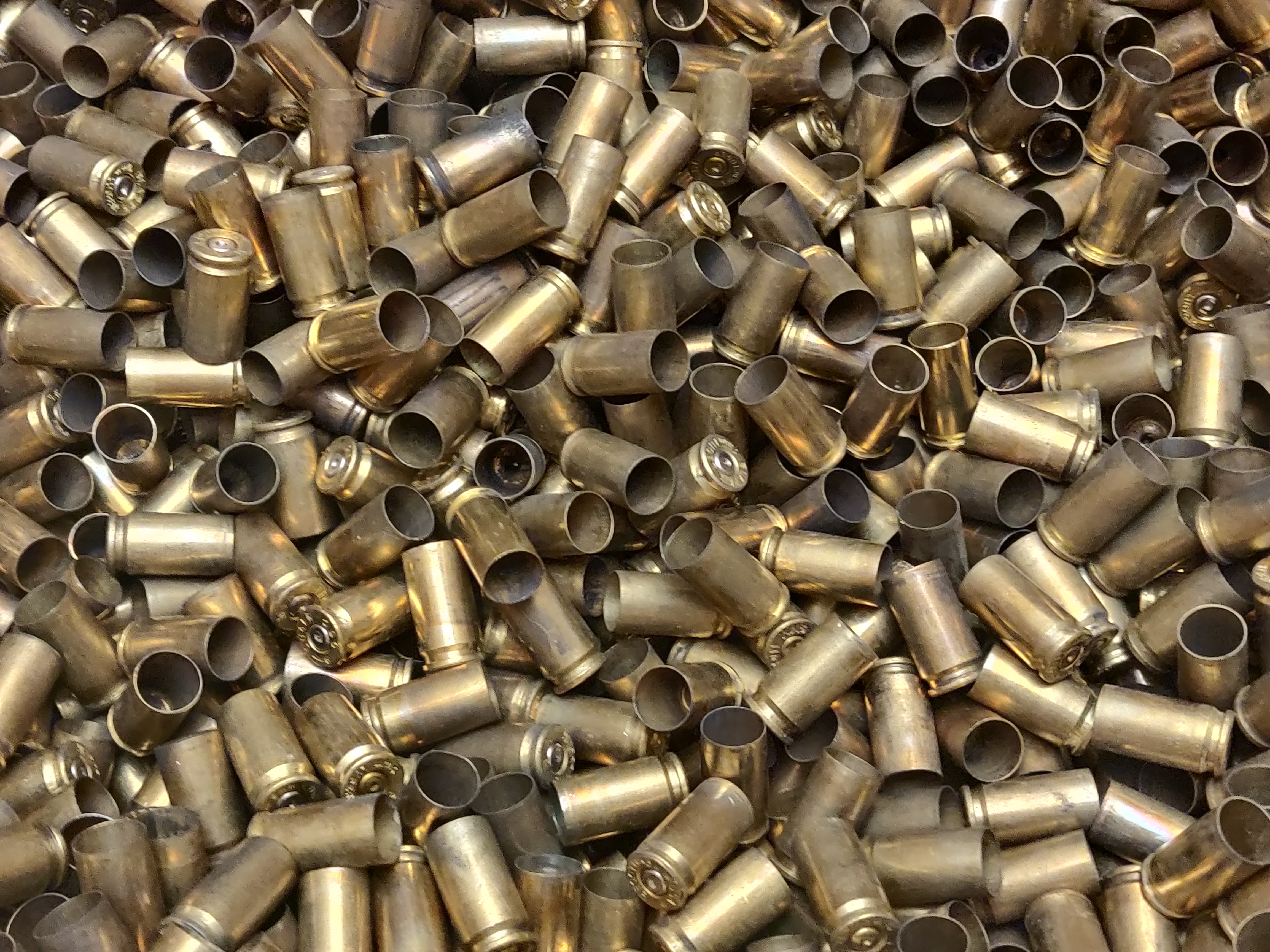
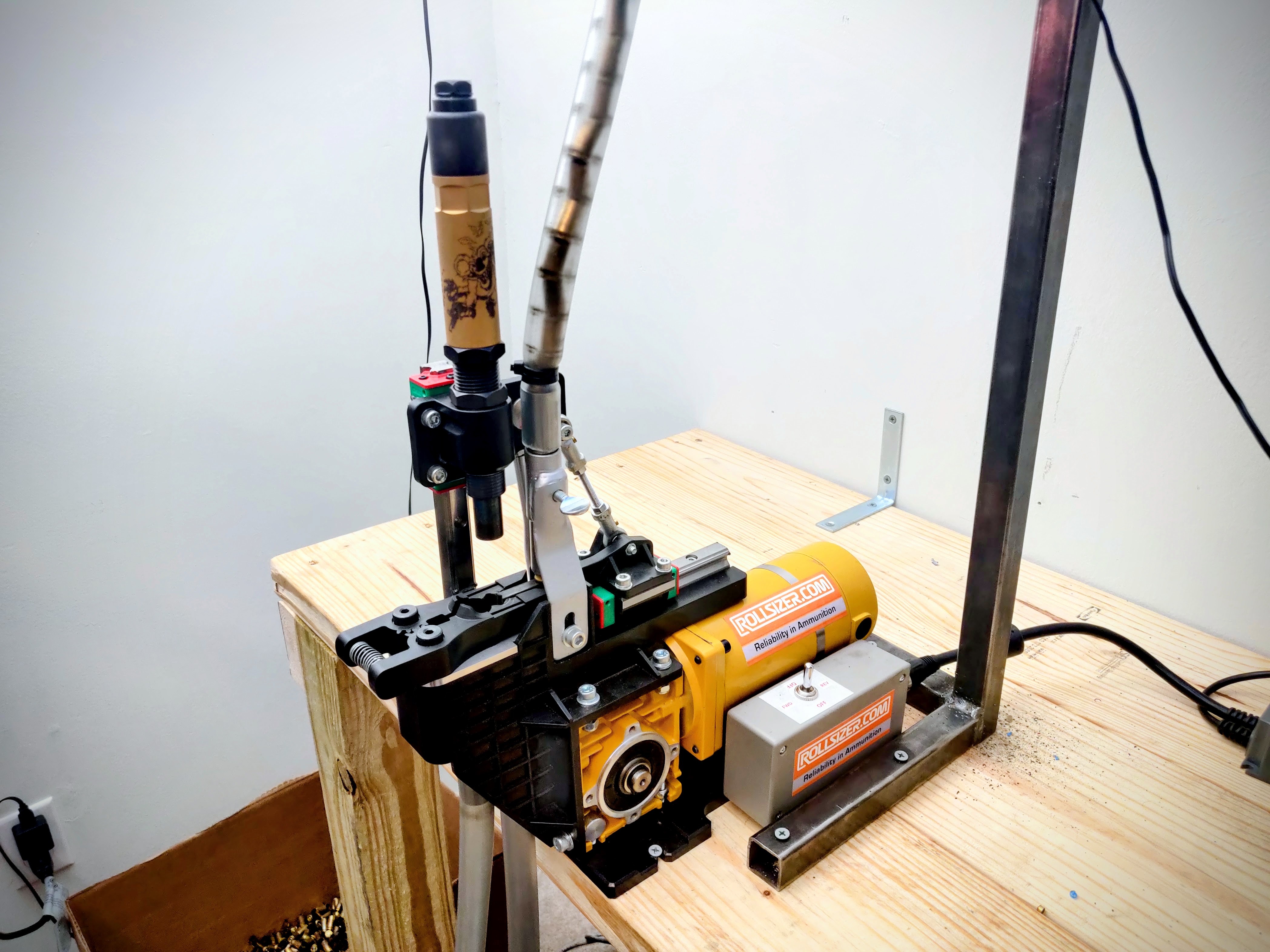
The dirty brass is "decapped," a process where we use a commercial unit to remove the spent primers from the cases.
Next the decapped brass is wet tumbled with stainless steel media and a detergent.
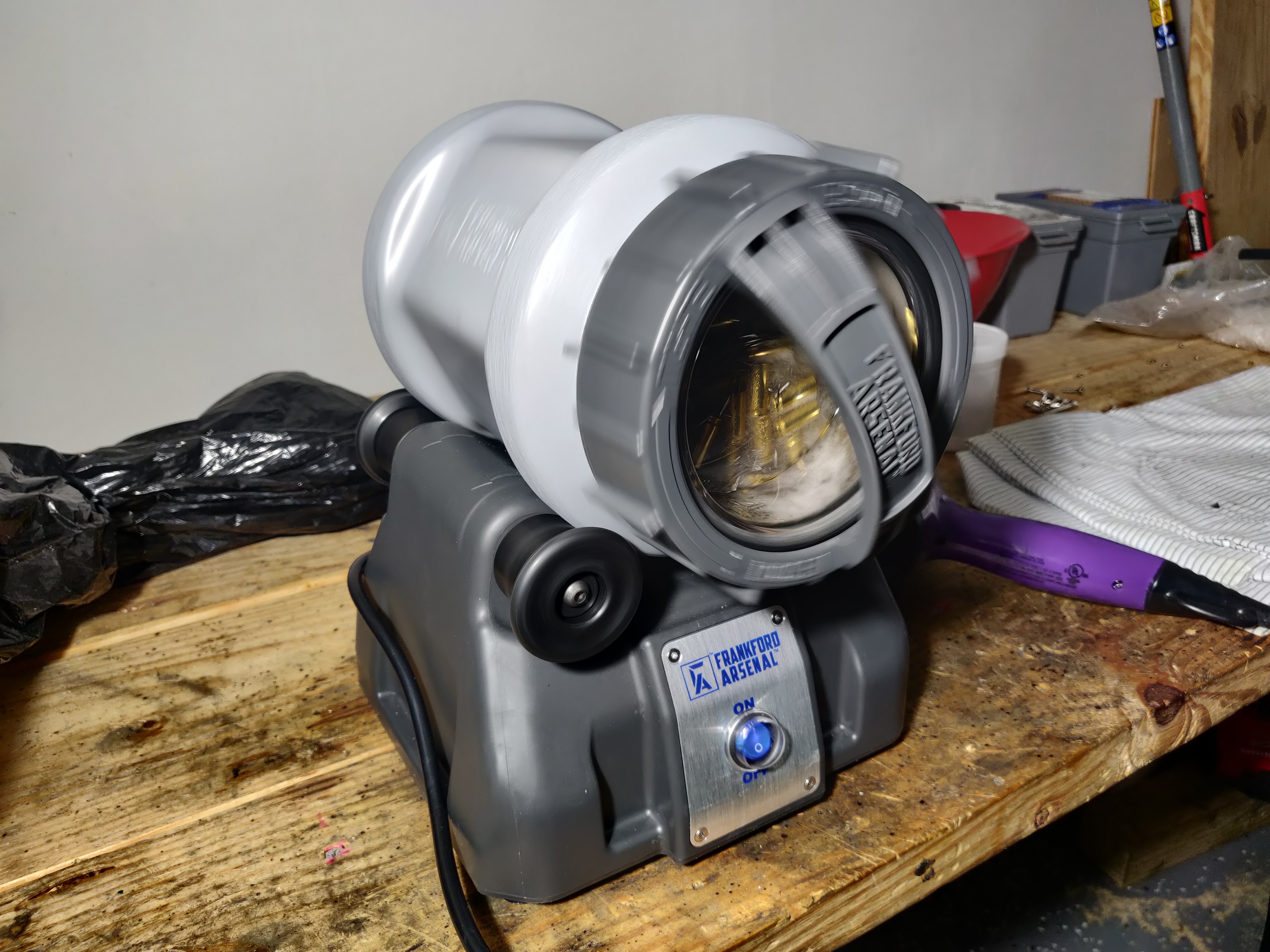
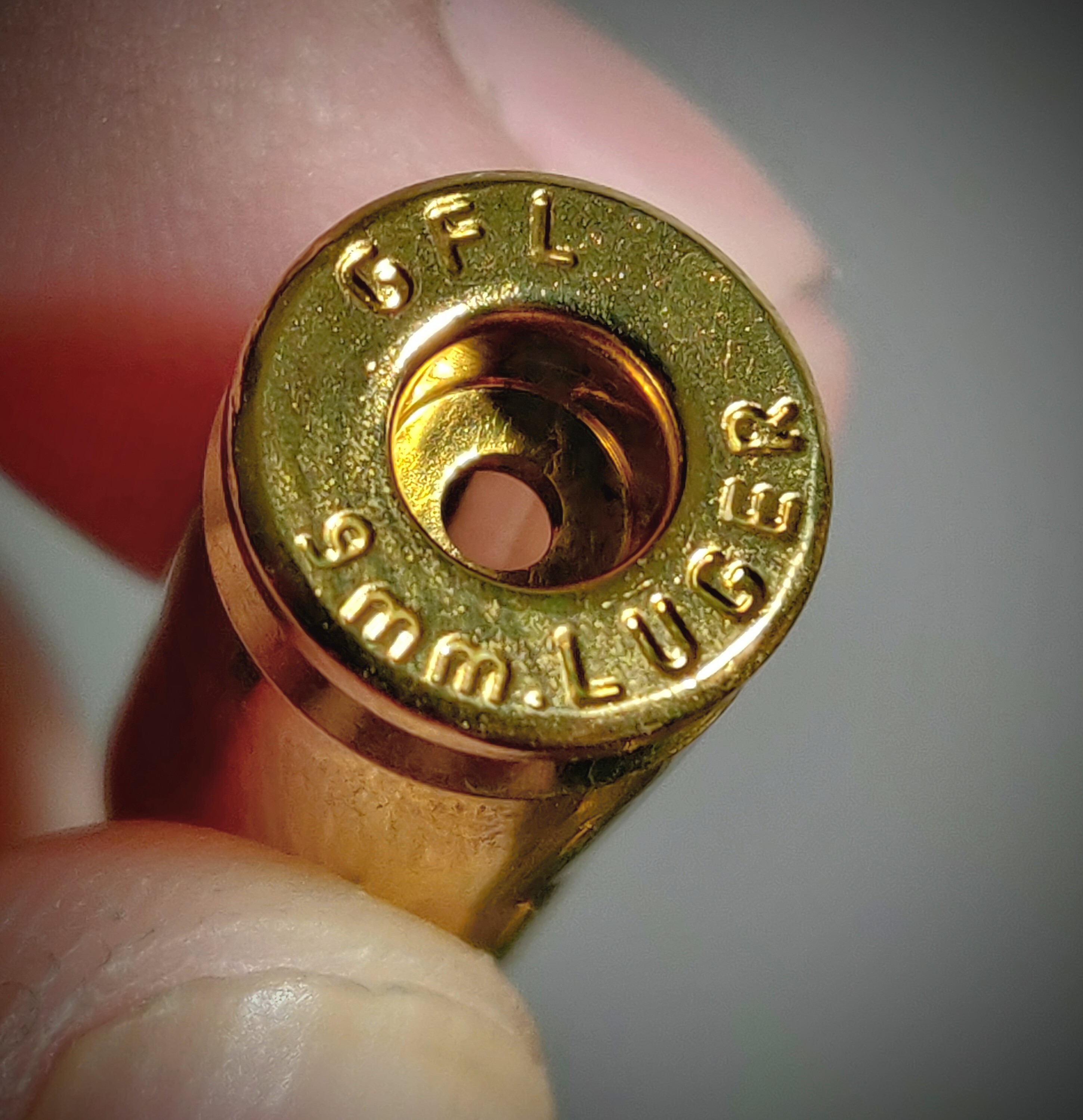
You can see the advantage of decapping prior to tumbling - a sparkly clean primer pocket! This brings a number of advantages, the primary of which is that it eleminates the risk of "crud" from the spent primer blocking the primer hole, which could cause a malfunction.
The brass is then roll-sized using a commercial-grade unit. Roll sizing is a process where the base of the case is "rolled" around a die to remove any "bulging" from the previous firing.
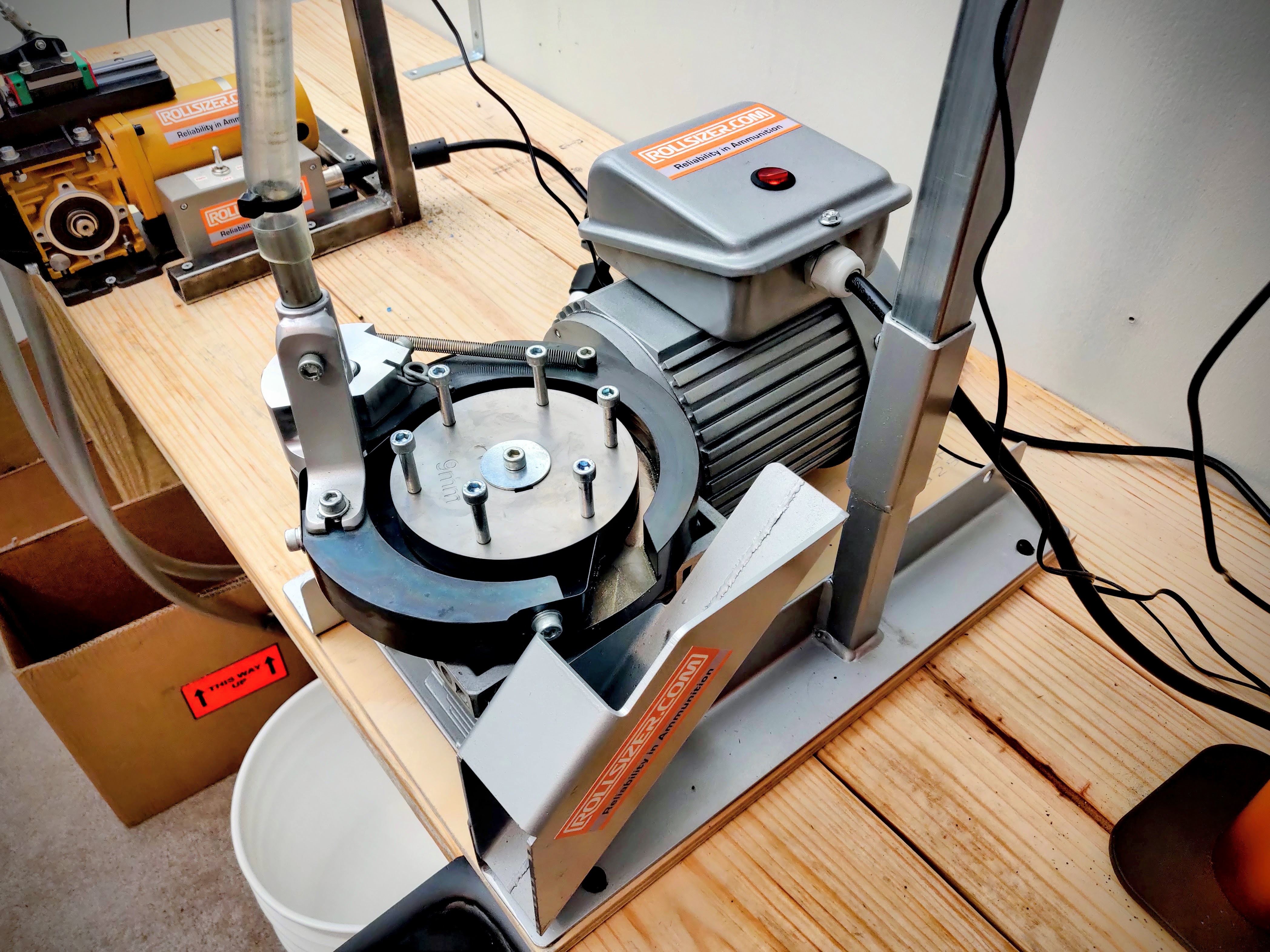
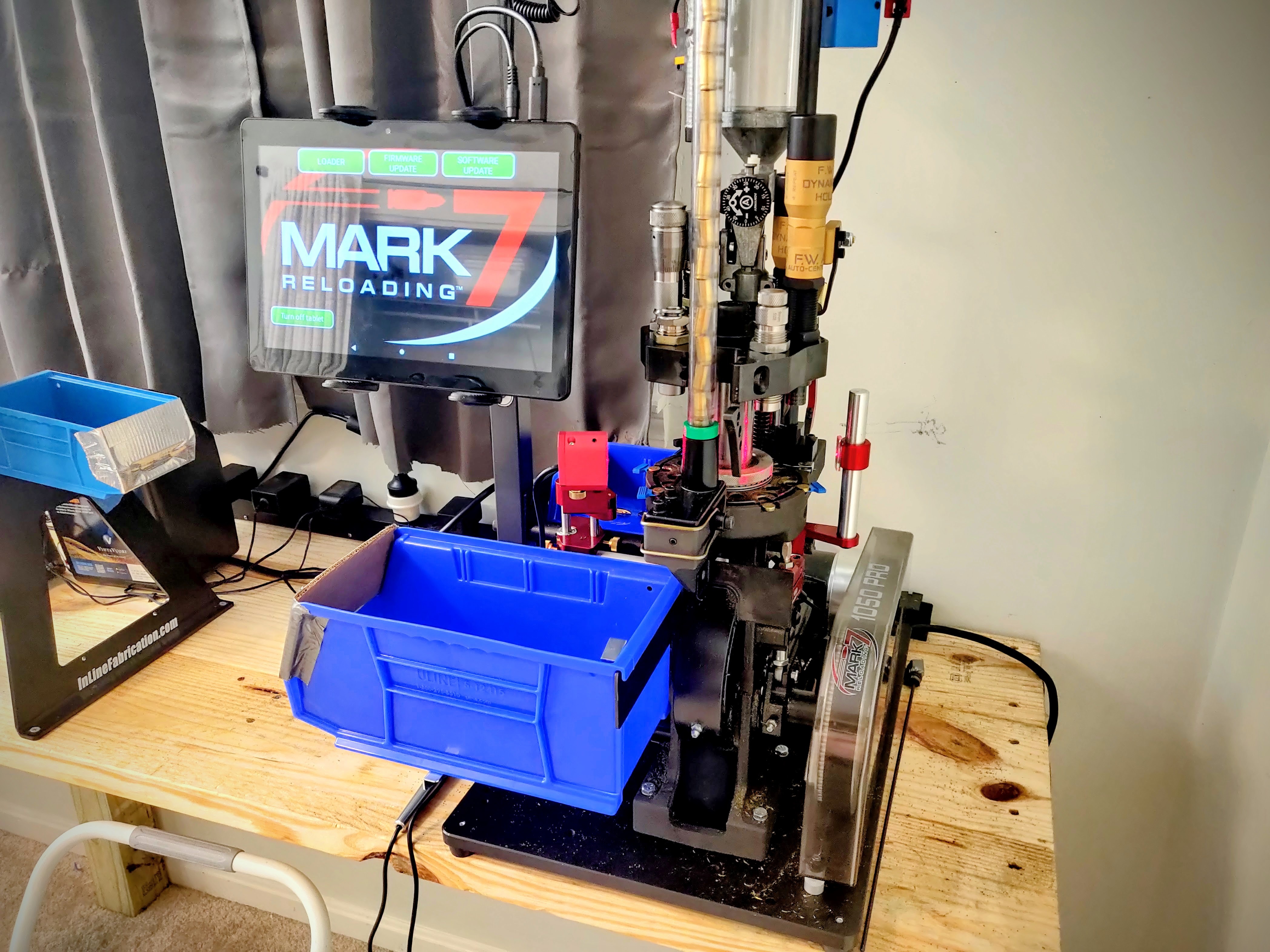
Now for the fun part! The brass is ready to load into ammunition. We use top-of-the-line automated loading equipment with many safety sensors to ensure maximum quality of our product.
At Rocket City Ammunition, we take quality control seriously. During the loading process, individual rounds are spot-checked for dimensional accuracy. This includes overall length, primer seating depth, and crimp amount. In the event a round fails this check, the entire batch is discarded.
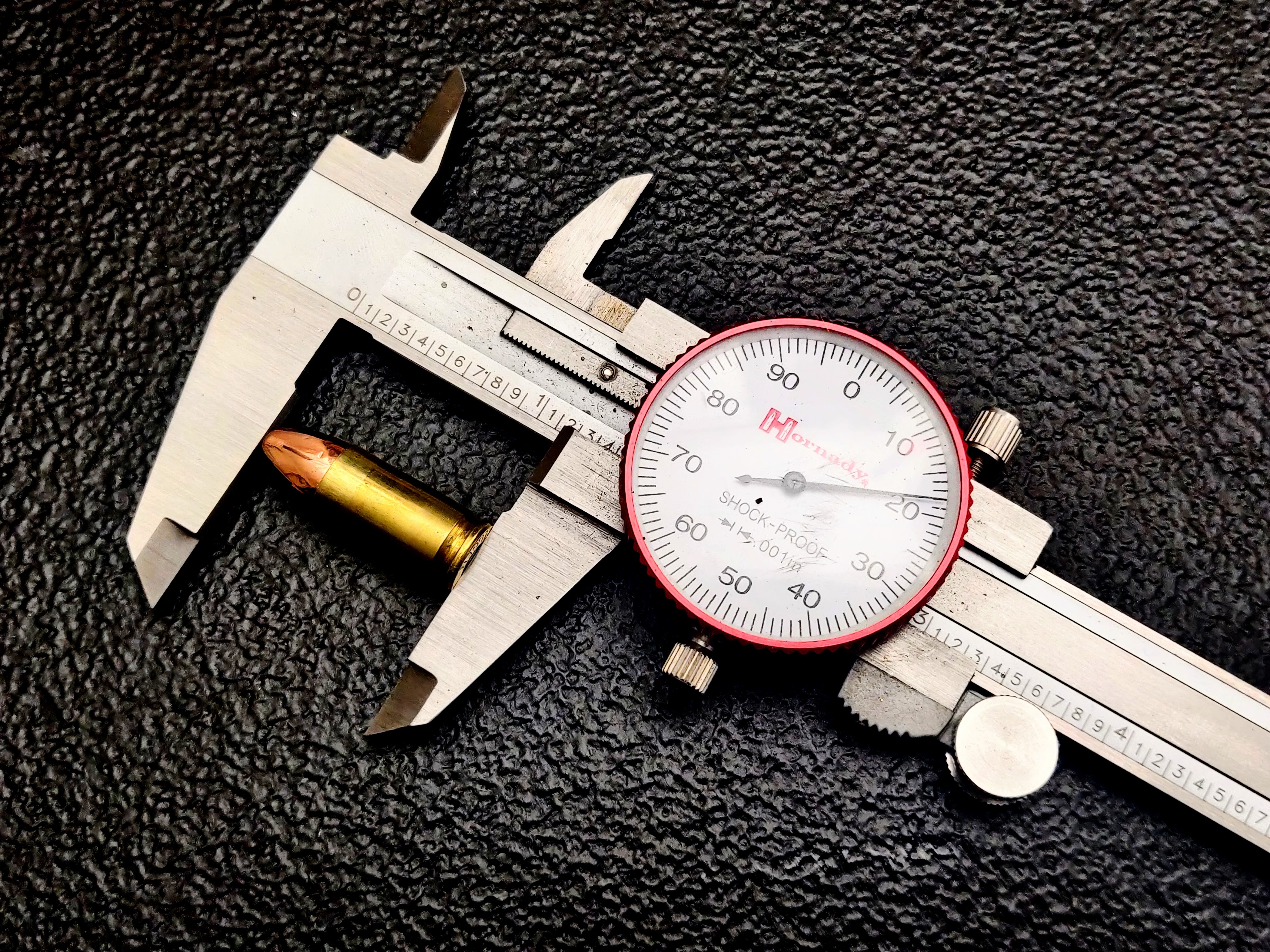
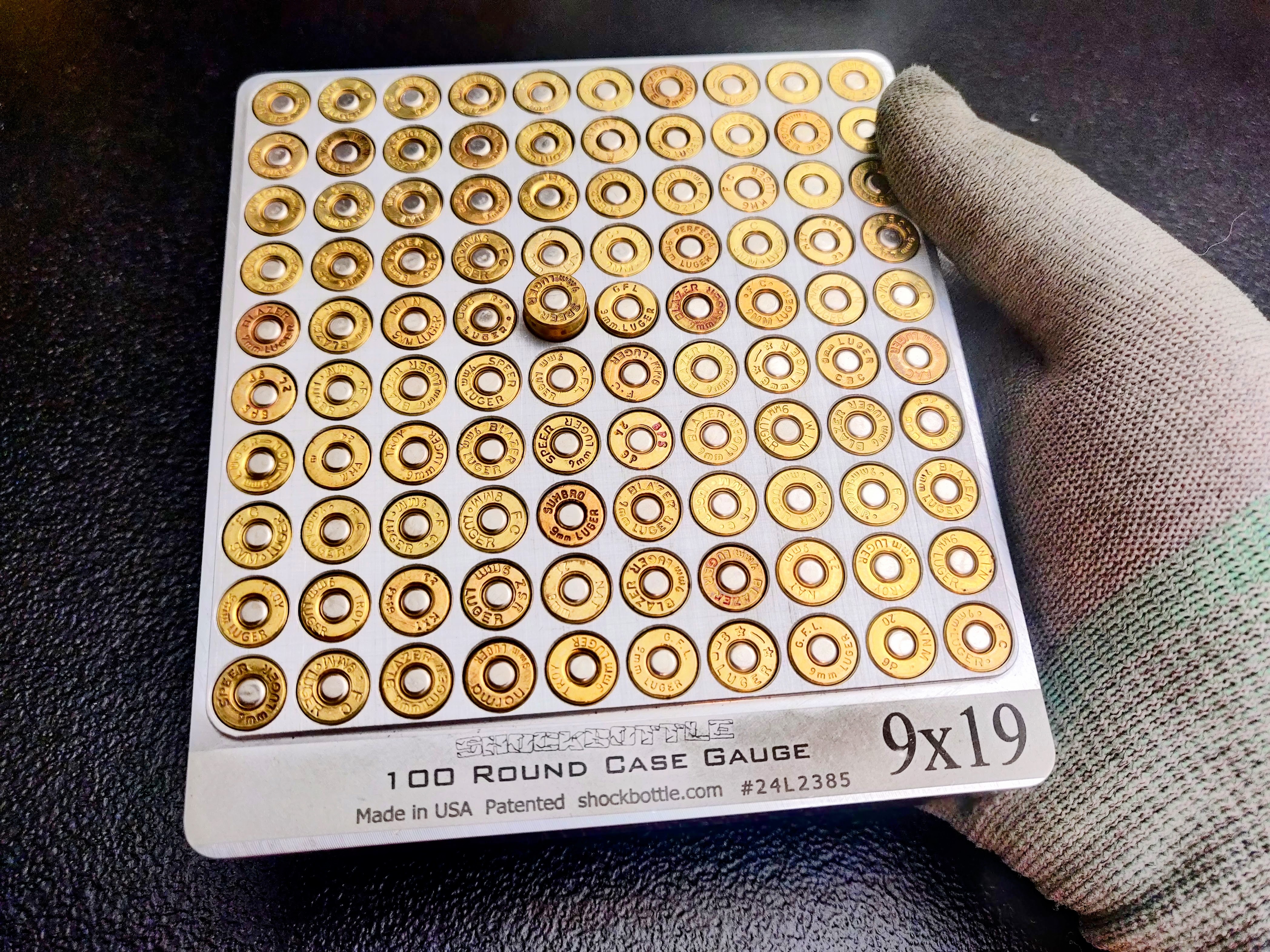
As a part of our quality control, we inspect every single round individually. We use a case gauge, a tool with dimensionally accurate chambers drilled into it, to ensure every single round will chamber into a minimum spec SAAMI chamber. We do the boring work so you don't have to!
Finally, the shiny ammunition is ready to be packaged and shipped! You can rest assured that Rocket City Ammunition is top-quality, ready to fuel your competition or just have fun at the range.
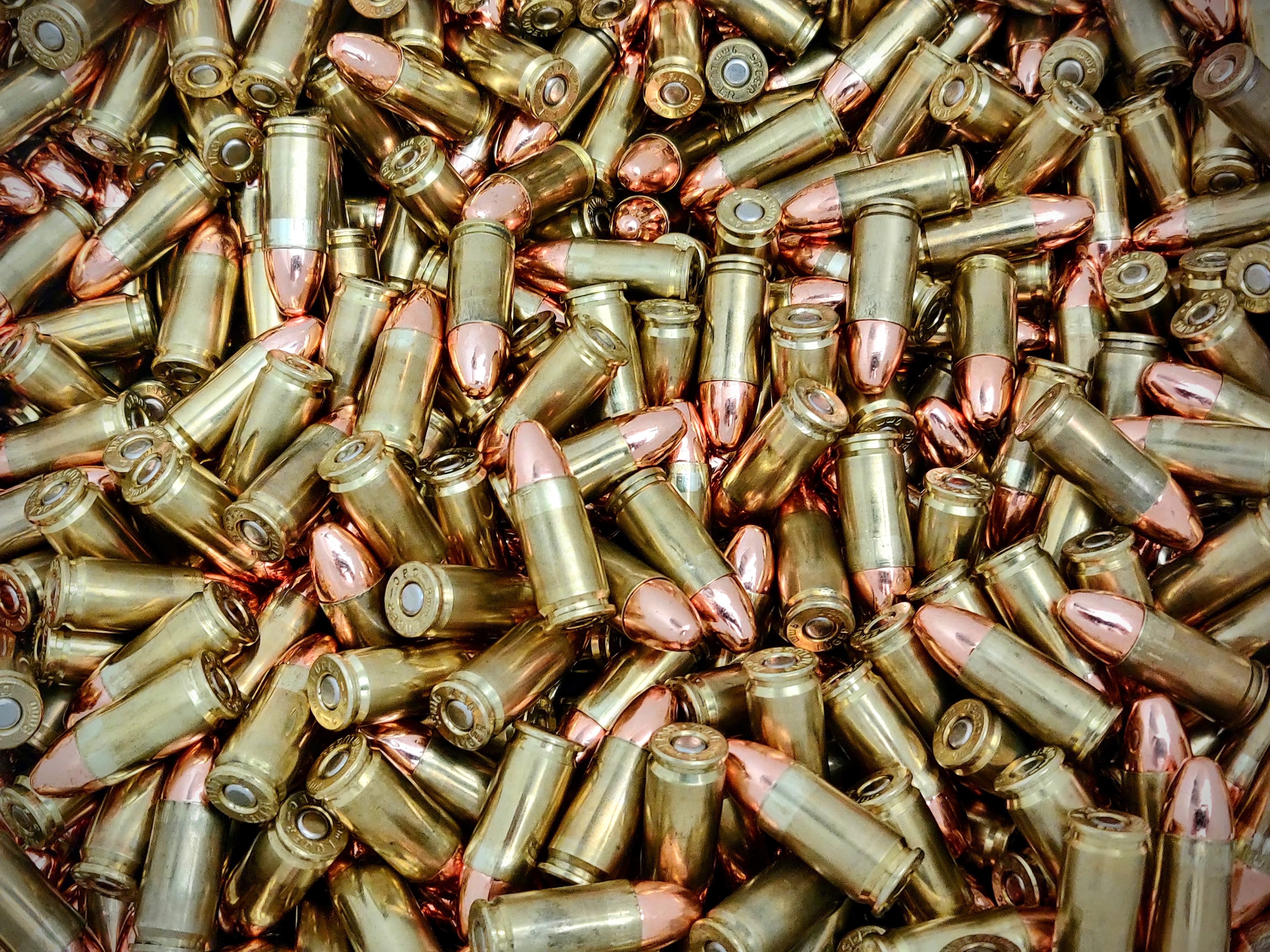